02. Transportation of Finished Products at Various Levels (Vertical, Horizontal, and Turned Paths)
Introduction: “FlexiPro,” a manufacturing company specializing in electronics, faced challenges in the efficient transportation of finished products between different levels of its production facility.
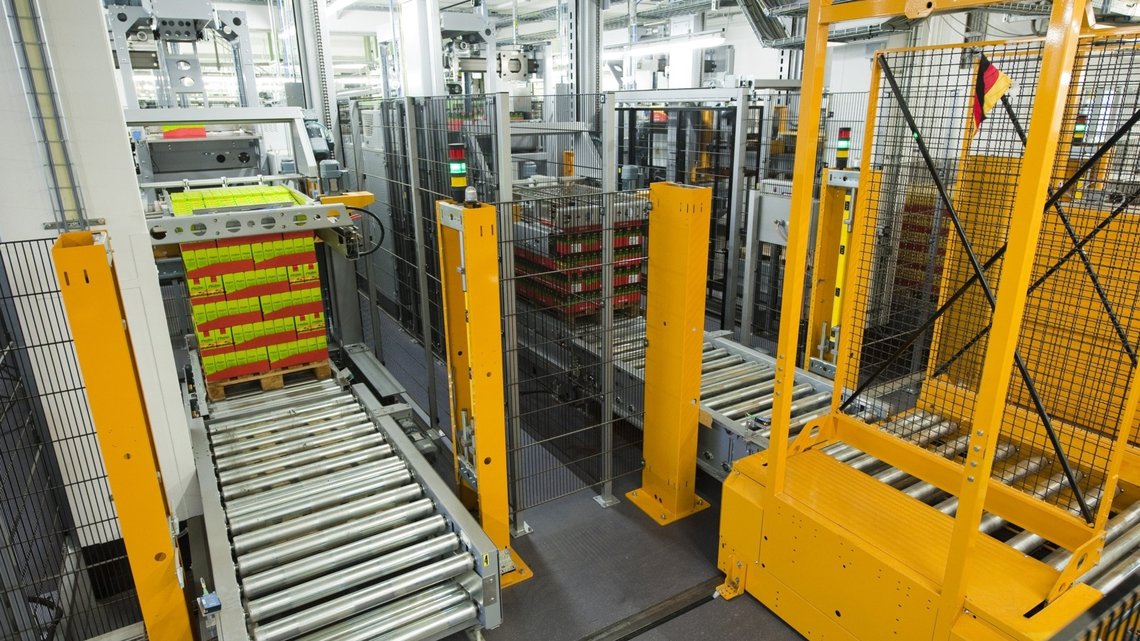