01. Conveyor automation of the production process
The production company “MetalTech”, specializing in the production of metal structures, encountered problems in the management of production processes due to the manual movement of workpieces.
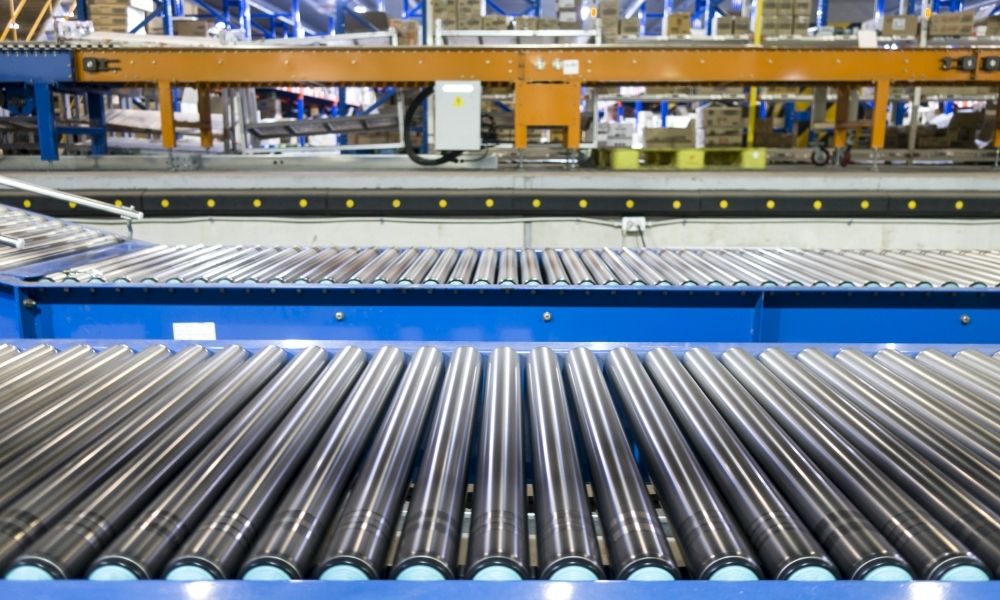
The production company “MetalTech”, specializing in the production of metal structures, encountered problems in the management of production processes due to the manual movement of workpieces.
Constant delays at various stages of production, an increase in the number of errors and a significant increase in operating costs. In addition, the company was unable to efficiently utilize production space due to limited manual labor capacity.
The company’s management set a task: to find a way to automate the internal movement of products to increase work efficiency, reduce logistics costs within the shops, and reduce the number of production errors.
After analyzing the needs of the MetalTech company, the KONSORT team developed a complex solution for automating the production process using conveyor systems. The project included the implementation of the following solutions:
The project from KONSORT helped “MetalTech” not only to improve production processes, but also to make the company more competitive in the market thanks to the optimization of costs and the improvement of the quality of customer service.
Do you have any questions? Get a free expert consultation